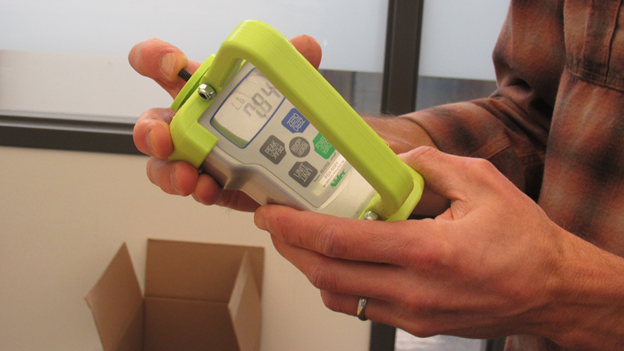
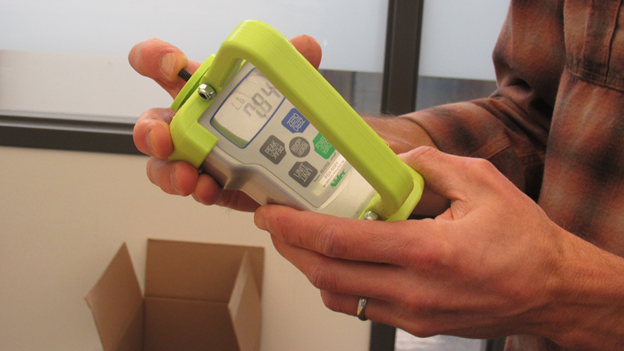
Scott Lindbloom, Suterra’s manufacturing engineer, inserts the force gauge into the Puffer® and easily clicks it into place. The gauge is quickly able to measure the motor power of the product, which is an important regular measurement for quality control. However, the most interesting thing about the measurement is not the force gauge itself, but the lime green casing surrounding it. It perfectly fits around the gauge and provides a handle for the otherwise unwieldy device.
The production of this seemingly simple casing had posed an interesting challenge for Suterra. Quality control has always been integral to the Suterra manufacturing process, and employees were completing this force measurement thousands of times a day. Therefore, employees needed to be able to replace these cases on the fly if something happened to them. At the same time, the casing and handle were such complex geometry that it wasn’t cost effective to use a prototyping machining service. For this kind of dilemma, Scott turns to the 3D printer.
Suterra’s 3D printers are perfect for building parts like these. An engineer simply creates a digital model of the eventual product, converts it to a format the printer can read, and sends it to the printer in the evening. The printer completes the product overnight and the engineer picks it up the next day.
“You just come in in the morning and it’s like Christmas!” Lindbloom says.
The 3D printers are also incredibly useful for creating prototypes of products. If something needs to be tweaked in a prototype, an engineer can easily make that change in a 3D modeling program and have the result in physical form the next day. In addition, the inexpensive nature of the polymer filament used means that 3D printing a prototype can save the engineers from costly future mistakes, especially if the final product is going to be made out of metal.
The actual printer is fairly simple as far as 3D printers go. It layers fine strings of lime green polymer over each other to create a lightweight plastic solid. Since virtually everything made by the 3D printer remains in-house, Suterra prioritizes function over an aesthetically pleasing final product. However, the models can be easily cleaned up with a razor blade when aesthetic polish is required.
“Anything you see in this bright green color was 3D printed,” Lisa Shinn, a product engineer at Suterra, says while gesturing to one of the printed parts. Indeed, there are a huge variety of objects in the telltale lime green, from clips to tubing to models of Puffers on display in the engineering room.
Although Scott is happy with the engineering department’s current selection of 3D printers, he’s excited about where the future of the technology may lead. He believes that future advances in 3D printing technology will not focus on the printers themselves. Rather, innovation will rely on expanding the materials that 3D printers can use, and making said materials available and affordable.
“For us, the technology will be in the filament.” he says. “Imagine someday having a metallized filament and a heated nozzle.”
Suterra makes an effort to continuously invest in innovation. The 3D printers are one example of the many ways that Suterra has been quick to incorporate new technology into the company, creating a company that will deliver new products well into the future.
For more information:
3D printing the first biomimetic tongue surface
How is 3D printer filament made?
After COVID-19, what does the future hold for 3D printing?
Researchers 3D print metal tusk caps to protect endangered walruses